The field of laboratory safety is very obviously about the protection and well-being of those who work within the labs. The topics of study within this field typically include chemical hygiene, biohazard safety, and even emergency management. One area of focus that historically has not been discussed under the lab safety umbrella, though, is workplace violence. Unfortunately, this topic definitely needs attention and a place among the other safety subjects.
Teaching laboratory staff how to recognize workplace violence (WVP) is important, and the activities that define acts of such aggression are numerous. The National Institute of Occupational Safety & Health (NIOSH) defines WVP as “any violent act, including physical assaults and threats of assault, directed toward team members at work or on duty and include physical injury, threats, abuse, hostility, harassment, discriminatory language/behavior and other forms of verbal violence that can potentially escalate to physical violence.”
The definition is important so staff can identify it, respond to it, and report it. A higher priority, however, is not only to learn the tools that will help staff recognize when potential threats at work arise, but to also be able to de-escalate a tense situations and mitigate any violence altogether. Teach laboratorians to pay attention signs of aggression such as disruptions, outbursts, throwing objects or threatening gestures.
Employees should be taught to respond to growing violence threats by remaining calm, listening, and by demonstrating empathy. Responding to people by yelling or getting into their personal space will only escalate the situation. Your tone of voice, the volume of your voice, your facial expressions and your posture all give signals to the person who is agitated, and if you respond inappropriately with these non-verbal cues, the situation could get worse. Training staff to de-escalate these situations can go a long way toward preventing certain violent incidents before they occur.
Unfortunately, part of the WVP program must be responding to active shooter threats. The Federal Bureau of Investigation (FBI) offers “Run-Hide-Fight” training that helps employees know how to respond when an active shooter situation arises. * There are details in the response that must be considered ahead of an incident. If you can run to an area of safety without getting hurt, go quickly, but do not try to coerce co-workers or patients to come with you. In these situations, you must first consider only your own safety if you wish to survive. If you are in a situation where you can hide in a safe place, be sure to turn off your phone and other electronic devices. Incoming calls can make noises which can alert the shooter to your position. If you must fight, use whatever you can find as a weapon, and fight to win. Do not give the shooter any opportunity to fire his weapon.
The laboratory may follow a facility WVP plan or it may create its own, but there should be a safety plan in place for such situations. Be sure to establish a strategy to identify and address the factors that contribute to violence throughout the workplace. Allow for and ensure prompt and accurate reporting of all incidents of violence including those that involve no physical injury. Empower leaders and employees with the necessary tools to eliminate violence in their areas.
The faster workplace violence can be detected, the sooner a good response may occur. However, as with personal wellness planning, prevention is always a solid approach. Avoiding violent situations altogether can be a part of the lab culture with regular education and training. Make sure there is a strong Workplace Violence Plan in action in your laboratory.
*https://www.fbi.gov/video-repository/run-hide-fight-092120.mp4/view
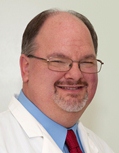
–Dan Scungio, MT(ASCP), SLS, CQA (ASQ) has over 25 years experience as a certified medical technologist. Today he is the Laboratory Safety Officer for Sentara Healthcare, a system of seven hospitals and over 20 laboratories and draw sites in the Tidewater area of Virginia. He is also known as Dan the Lab Safety Man, a lab safety consultant, educator, and trainer.